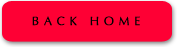
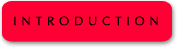
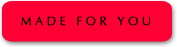
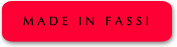
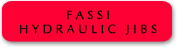
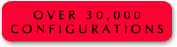
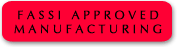

 |
Among the characteristics that distinguish a Fassi crane on the market there is certainly
a special commitment to quality in every technological and constructional aspect,
which takes concrete form in machining processes that are perfected directly within the
company. These are the fruit of exclusive know-how from the sector, and the results
are only approved if they comply with the severe expectations set for each phase.
Among the fundamental points in this commitment is the choice and processing of
metals, and in particular special steels, which are selected and processed so as to
form a true production cycle, with levels of excellence that deserve to be more widely
known Let us now take a look at some of the attention dedicated by Fassi to metals, as
they are gradually transformed from “raw material” into a crane: casting and welding
processes, bearing in mind that these too are required to comply with precise and
extremely strict quality parameters, rigorously tested and checked, so that each individual piece is "approved" by Fassi.
Casting of bases and columns
The crane bases and columns is an excellent example of how Fassi approval is applied and what it involves. Cast elements
are made from special steel and cast iron, and many have extremely high mechanical characteristics, comparable
with those of metal sheets with high elastic limits. The majority of the alloys used in casting are defined directly by Fassi,
in co-operation with specialists in these processes. The entire casting system of potential suppliers is analyzed by Fassi
technicians, and only if considered capable of respecting and providing a long term guarantee for specifications, in terms
of all casting characteristics (chemical, mechanical tenacity, health and safety...) will the foundry be "Fassi approved".
Fassi's know-how is also of fundamental importance to discriminate between, and thus provide an objective evaluation
of, the methods used by the supplier, from casting procedures to forming (empty form created from sand/resin which is
filled with the molten metal during the casting process), to the various finishing operations, to heat treatment and nondestructive
and laboratory testing. According to the methods used the results obtained may be quite different, and over
the years Fassi has identified and perfected which of these parameters are ideal. Again bearing in mind that excellence
means first of all preventing the faults typical of casting (such as cracks, inclusion of foreign bodies, shrinkage, bubbles...),
the processes are approved casting by casting, with an extremely wide-ranging series of tests. These start from
sectioning of prototypes and continue with a range of non destructive tests (control using magnetic particles, penetrating
fluids, ultrasound, rays) in search of possible internal and surface faults. It then proceeds with analysis of material characteristics
(chemical analysis, metal analysis, hardness tests, traction tests, resilience tests...). Each single casting is
only approved if all the test results comply with Fassi specifications. All this commitment is justified by the target that
Fassi has set itself: using monolithic cast components it is possible to obtain the ideally shaped base, column and other
components, according to the stress to which the crane will be subjected. This makes it possible to achieve levels of reliability,
particularly in the long term, that would be impossible using welded components. This is why Fassi has adopted
cast elements in almost all its products.
The welding process
It is clear that the characteristics and end quality of welding operations also depend first of all from the materials to be
welded together: this is why Fassi makes a careful selection of the suppliers of special steels. The secret of a perfect
weld then depends on setting the process parameters exactly: Fassi uses a continuous semiautomatic, automatic and
robot controlled "mig mag" gas arc-welding process (using active-inert gas) which, because of the types of material and
thicknesses involved, reduces the faults typically found in other types of welding processes. All those machining operations
and actions carried out before welding, such as preparation of the parts and study and creation of specific equipment
and systems to position and lock the edges to be joined, also fall within the company's range of activities. Equally
important is the choice and definition of welding parameters, such as electrical parameters (volts, amps), the speed of
advance of the welding torch and the solder, the movement of the torch, the distance between the torch and the piece.
But equally important are the gas type and flow rate, and the type of solder used, according to the materials to be joined
and the type of joint. The delicate nature of this process and the exclusiveness of the Fassi procedure lies in setting out
all these parameters, on which the end result depends, in the ideal way. It is also of fundamental importance for specialist
technicians to carry out inspections during the operation, to ensure that the parameters set in the procedures are
complied with and to carry out non destructive and laboratory tests for continuous process monitoring. The aim is to
guarantee the required quality in terms of the shape, size, resistance and tenacity of each joint.
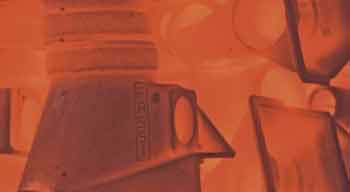
Treating
Once the steel casting (in the case of cast iron the process
is different) has been broken out of the mould and flogged,
it is freed from the feedheads and casting channels and
subjected to an annealing process. At this point the non
destructive tests on each individual raw component begin:
using magnetic particles, penetrating fluids, ultrasound and
X-ray. After any repairs (only foreseen for steel castings)
the raw component is then subjected to thermal treatment
cycles, which may be for normalization or tempering and
hardening, to give the piece the mechanical characteristics
and resistance required by Fassi specifications. After these
operations, final tests are carried out both on the pieces
and on the samples. The samples are normally tail
elements that are cast with the pieces, and therefore
undergo the same cycle. At the end these tail elements are cut away from the casting, and the samples taken in this way
are used to carry out the traction, resilience and metal analysis tests to ensure that the material complies with the
necessary specifications.
Welding
In Fassi, welding is mainly carried out using very high technology automatic and robot
controlled systems, capable of ensuring perfect replication of the parameters foreseen
by the process. Whether it is done by a robot or by a specialist welder, they are still an
integral part of the Fassi "approval" process. This means that both the technicians programming
and managing the systems and the welders themselves are suitably trained
and qualified to comply with the process requirements that characterize work here in
Fassi, whatever the conditions.
|