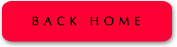
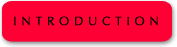
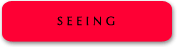
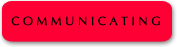
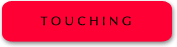
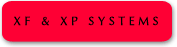
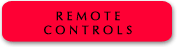
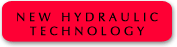
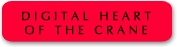
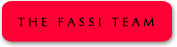
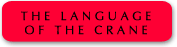 |
An intelligent system perceives things, understands them and takes them in
From the software point of view, Fassi's research is significantly revolutionizing the approach and the electronic technology
that has been used until now in the truck-mounted cranes sector. The innovative integrated and intelligent IMC
(Integrated Machine Control) control system is a real brain that knows how to coordinate all the extraordinary power that
is available thanks to the synergy between the most advanced electronic systems and the latest hydraulic systems. The
IMC system works exactly like the nervous system of a living being and has an electronic brain (master unit) at the centre
of its own system which can process in real time an enormous amount of information coming from peripheral sensors
and from the electro-hydraulic systems of the crane. This new software is much more powerful, but at the same time
more intuitive and easy to manage, as well as being user friendly, and structured with a greater number of operational
control parameters of the crane. The IMC system coordinates, manages and controls the operating functions of the
crane, sending the data by CANbus from the various equipment and devices. The system is therefore able to select the
best conditions in relation to the work to be performed, to detect possible problems and automatically control them, ensuring
optimum performance in accordance with any specific load or movement situation. This works hand in hand with
the ADC (Automatic Dynamic Control) system that is set up to control the dynamics, and which allows the maximum
speeds to be achieved in relation to the load being maneuvered. Thanks to the ADC system there is a greater oil flow
through the hydraulic distributor and consequently better multi-functional performance and higher working speeds, to the
extent that when the induced load on the lifting rams changes, the speed of movement of the crane is automatically
managed within the set parameters.
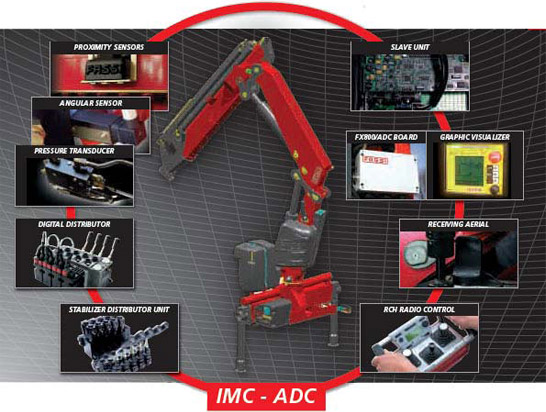
Everything under control, including stability
The IMC system, integrated into the ADC system, is directly and constantly interfaced with the control and radio control
devices of the crane. The entire operational state and functionality of the crane electronics can be checked in real time
on the digital display of the radio control and on the panel of the machine itself. Thanks to the power of the IMC system,
all of the crane functions are constantly shown on the display in exactly the same way as in the cockpit of an aeroplane.
Also thanks to the IMC system, the activation of the outriggers can be checked and specific commands given, including
any further stabilizing operations, all at the same time.
The digital "brain" that coordinates the Fassi electronics is the result
of our vast experience in management software: a master unit that is
capable of processing an incredible amount of information in
milliseconds.
Inside the Fassi digital system: innovation at all levels
The innovative electronic components used on Fassi cranes have made it possible to fit multi-functional distributors with
the most advanced hydraulic solutions for performance and reliability. The electro-hydraulic modules of the distributor
with CANbus technology, for example, can communicate with the central processor unit and agree on the actuation of
the Electronic Flow Sharing device. This system distributes the oil that comes from the pump proportionally to all of the
maneuvers that are being actuated at any one time. In fact, using a Fassi crane fitted with the new Flow Sharing system,
it is possible to actuate several levers at the same time and generate different movements redistributing the available oil
flow proportionately to all the movements that are being actuated, ensuring the execution in each case. The digital electronics
are again essential in terms of the synergy between the pressure transducers installed on all of the rams and the
sensors. In particular, the angular sensor is able to recognize the position of the load to make the system genuinely intelligent.
In fact, in overload conditions, read by the transducers, the sensor authorizes the maneuverable functions and
blocks those that would increase the overloading. Furthermore, it controls the safety management of the ProLink system.
All of this is made possible by the interface between the Slave Unit that transfers in CANbus the data sent in analogue
form, and by the new electronic card the genuine "brain" of the whole system. The card has a new generation double
microprocessor to ensure crosschecking and obtain the maximum safety levels in all operating conditions.
Before any item is put into production it has been subjected to the most severe mechanical, vibration and temperature
tests. Even the housing guarantees the highest levels of protection against adverse atmospheric conditions (such as
water and dust). Furthermore, the card is protected by an anti-condensate filter: a special unidirectional drain plug that
prevents the formation of condensate inside the box. The meticulous attention paid to the quality of the internal electronic
components also stands out with respect to the connectors, specially designed for automotive applications and IP 67
certified, equipped with bolted-on fastenings to guarantee a good contact even when subjected to the most severe levels
of vibration. This higher reliability stems also from the fact that the connectors must never be opened. In fact, even when
the crane is being assembled, they are installed already closed with the appropriate external clamps.
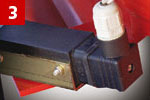
1. PROXIMITY SENSORS
If required, they limit the rotation arc of the crane, always guaranteeing the stability of the truck, or they activate a
differentiated torque limiter on the unstable working area.
2. PRESSURE TRANSDUCERS
Fitted on all the lift rams of the crane, they control the pressure induced by the lifting in the ram.
3. ANGULAR SENSOR
It recognizes the position of the load, making the system intelligent: it authorizes the maneuverable functions and blocks
those that would cause an overload.
Incredible versatility and full self-diagnostic capacity
The new electronic systems on the Fassi cranes let you use a multitude of advanced functions, as well as the main ones
for the management of the crane or the load control systems. In this respect the possibilities of monitoring the stability
conditions of the truck/crane unit, the transmission of data regarding the working pressure and the lifting capacity of each
individual ram, the management of the torque limiting device of the winch, and the information that is necessary for managing
the crane in a safe manner also when there are mechanical extensions, really stand out.
Furthermore the IMC is configured as an open system and has memories that can be implemented in time: it is able to
store data on the operation of the machine and allows you to run checks, monitoring the state of efficiency of the crane
even on a PC or palmtop (PDA), and it is already set up for technological and functional updates resulting from further
advances in electronics. The management and the modification of the operational parameters for updating and customizing
the operational functions is as a result made much easier because you don’t necessarily have to use a PC; you can
gain access to the programming function directly from the control handle of the radio control or from the main control.
The stored data is obviously still password-protected.
Fassi's technological progress, characterized by the use of a new electronic management
system, makes the most convenient and simple interfacing possible also when monitoring
operating reports to be aware of the state of efficiency of the crane and schedule maintenance
intervals, in real time.
|